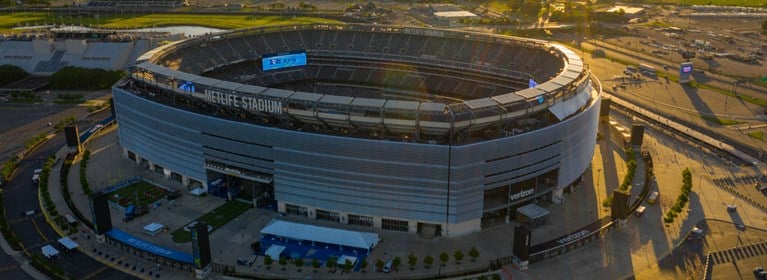
Entertainment | Power & Motion Technology | By Jason Wills | 01 Jan 2019
THE CHALLENGE
Scoreboards and screens are strategically placed throughout modern sports stadiums. They are used to display scores, stats, and game clocks, which greatly enhance the fans experience and keep the fans aware of what’s going on in the game. Most major sports stadiums have become multi-functional venues. When stadiums are not hosting sporting events they can be used for charity runs, concerts, youth sports, or other large events. These events take advantage of the numerous scoreboards as well.
With so many scoreboards and screens, especially those at ground level, moving equipment and personnel in and out can be problematic. These scoreboards need to be raised or moved to allow pedestrian foot traffic or equipment to be moved into and out of the stadium.
Moving these scoreboards and screens is no easy task. Modern scoreboards are similar to extremely large, high definition TVs. Some more than 20 feet high, 20 feet wide, and weighing several thousand pounds. Adding to the physical complexity of moving these scoreboards and screens is the fact that they must be synchronized to raised and lowered level. If the screens or scoreboards are raised unevenly the structure or screen may crack.
THE SOLUTION
Duff-Norton’s automated actuator systems (AAS) are the perfect solution to these types of problems. Duff-Norton’s robust actuators along with closed loop controls can easily lift and lower loads. Duff-Norton proposed an AAS system using two linear actuators and controls to synchronously raise and lower the scoreboards. Each actuator is capable of moving a 2 ton load. The actuators consisted of integrated end of travel limit switches as well as encoders for positional feedback to the controls system.
OUR ADVANTAGES
There are several advantages to Duff-Norton’s AAS. Our systems are completely designed and tested to meet the specific needs of each application. Outdoor sports stadiums require water tight enclosures and connectors. Duff-Norton’s AAS controls enclosure and electrical connectors were all designed to meet NEMA Type 4 rating. The actuators used bellows boots and special outdoor epoxy paint to keep water and debris from entering the jack.
Scoreboards and screens must occasionally be removed for maintenance. In order to accommodate this scheduled maintenance the actuator motors, limit switches, and encoders were designed with quick disconnects at the controls enclosure. This allowed the system to be quickly removed and installed without having to wire and unwire the controls.
The controls for the AAS used encoder feedback from each actuator to compare the position of each actuator. The system was designed to hold a synchronization tolerance between the actuators to within +/- 0.25 inches. If the system detected that one actuator were ahead of the other actuator when raising, the system would then stop that actuator and allow the actuator that was behind to sync back up.
Contact Our Engineering Team For A Free Application Analysis
Duff-Norton Movable Stadium Scoreboard
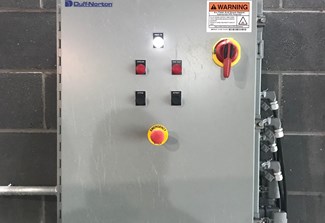
Related Articles
Duff-Norton Screw Jacks Lift U.S. Navy's Electromagnetic Railgun
Naval Surface Warfare Center
From the muzzle-loading cannons of the USS Constitution to the Advanced Gun System on the U.S. Navy-built Zumwalt-class destroyers, naval warfare has always relied on explosives to fire projectiles at the enemy. A proof-of-concept railgun, elevated by two Duff-Norton Mechanical Actuators, can accelerate a projectile up to Mach 6 and fire it more than 100 nautical miles.
Kern Steel Fabrication, Inc. is a well-known structural steel fabricator located in Bakersfield, CA. One of their specialties is aircraft maintenance systems. Kern Steel was recently asked to develop an aircraft maintenance system that would accommodate various aircraft models. This system required a combination of walk ways, stairs and working platforms along with the ability to adjust the height of each platform in order to reach standard maintenance areas from cockpit to tail.