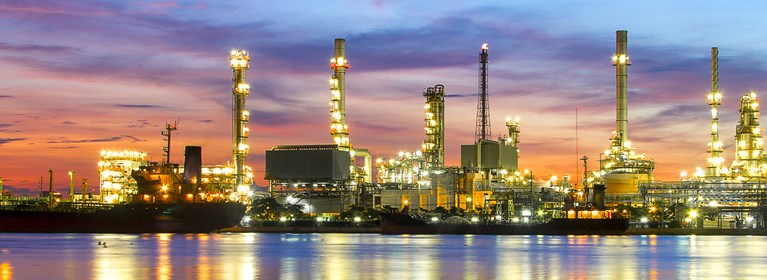
Sistema automatizado de monorraíl de línea de pintura de ruedas y puntales
Fuerza Aérea de los Estados Unidos
Automotive Industry | Manufacturing | Aerospace | Sistemas de grúas | Power & Motion Technology | Lynn Bostrom | 24 nov. 2009
El grupo de mantenimiento de aeronaves de esta Base de la Fuerza Aérea de los Estados Unidos se enfrentó a un aumento significativo de las cargas de trabajo, pero no a un aumento del personal o del área de trabajo. Esforzándose por proporcionar piezas de aviones a reacción de calidad, a tiempo y dentro del presupuesto, se implementaron principios de Lean Manufacturing en la instalación para reducir los días de vuelo y aumentar la productividad a través de la reducción de residuos.
Cada área de mantenimiento se mejoró a través de la participación de los empleados y la gerencia en los equipos de mejora de procesos. Se estudiaron las áreas de trabajo, se discutieron y analizaron las ideas, luego se aplicaron los principios de Lean Manufacturing en toda la instalación. El objetivo final del proyecto general de transformación Lean era mejorar la productividad con cero horas extras.
Se diseñó e instaló un sistema personalizado de entrega de materiales aéreos que automatizó e integró nueve transportadores de monorraíl aéreos desde dos líneas de entrega de ruedas y puntales separadas a través de un solo proceso de línea de pintura compartida. La experiencia en aplicaciones de Magnetek se proporcionó para cumplir con los objetivos de este proyecto general de transformación Lean.
Magnetek diseñó un sistema de control de monorraíl personalizado que simplificó y automatizó el proceso de la línea de pintura de ruedas y puntales. Los portadores de monorraíl fueron alimentados por variadores de frecuencia ajustables IMPULSE® que son capaces de trabajar en una variedad de entornos de alto rendimiento. Los accionamientos IMPULSE no solo están diseñados específicamente para aplicaciones de grúas y polipastos, sino que también ofrecen más versatilidad que los controles de contacto tradicionales y una huella más pequeña para una instalación flexible. Se utilizaron controladores lógicos programables (PLC) para ejecutar la parte de automatización del sistema.
Se instaló un sistema de barras conductoras FABA de bajo perfil para la potencia y el control de la línea integrada. Este sistema de barras conductoras facilitó la producción y entrega justo a tiempo requerida por el usuario final. Además, se deben cumplir estrictas pautas de seguridad, y FABA está diseñado para garantizar la máxima protección contra el contacto eléctrico accidental, ya que la barra conductora está encerrada en una carcasa de PVC que no es inflamable y resistente a los productos químicos. FABA también cumplió con las estrictas pautas de eficiencia del usuario final, ya que su diseño garantiza un contacto eléctrico continuo y un control de carga máximo sin cadenas, correas o piezas móviles, lo que reduce la necesidad de mantenimiento.
Se implementó una combinación de un sistema de control de radio de 18K con transmisores de radio SLTX y estaciones de botón de operador montados en fijos para la intervención en todo el sistema. El receptor de 18K fue diseñado a medida para cumplir con las especificaciones de la aplicación. Los controles de radio remotos inalámbricos de servicio pesado SLTX fueron elegidos porque están diseñados para soportar entornos hostiles y usar interruptores de función auxiliar de grado militar, cumpliendo con los requisitos del usuario final.
Dos estaciones de pulsador para control manual instaladas en las cabinas de pintura son las estaciones de trabajo clase I, Div. 1, intrínsecamente seguras cumplen con las especificaciones de seguridad. También se instalaron dos pantallas táctiles de computadora de interfaz hombre-máquina (HMI) para imputar datos e informes de estado del sistema. Cada uno de los nueve operadores en el sistema utiliza la tecnología de identificación por radiofrecuencia (RFID) como identificación para una mayor eficiencia.
Artículos relacionados
Sistema automatizado de monorraíl de línea de pintura del motor
Caterpillar, Inc
Mejorar la flexibilidad de fabricación y proporcionar capacidad de producción adicional fueron los objetivos de la iniciativa de la línea de producción de las instalaciones de Caterpillar en Lafayette. El equipo de Magnetek diseñó un sistema de monorraíl automatizado que elimina el tiempo de inactividad, el retrabajo y el exceso de inventario.
Puente de mantenimiento de prensa de freno automatizado
Federal-Mogul
Como medida de reducción de costos, un fabricante de autopartes quería reducir la cantidad de personas y el espacio requerido para fabricar pastillas de freno. La solución implicó la creación de pequeñas células de trabajo dentro de sus instalaciones de fabricación. Su sistema fue mejorado utilizando magnetek AC Drives, PLC Controls y nuestro sistema de auto-despacho.