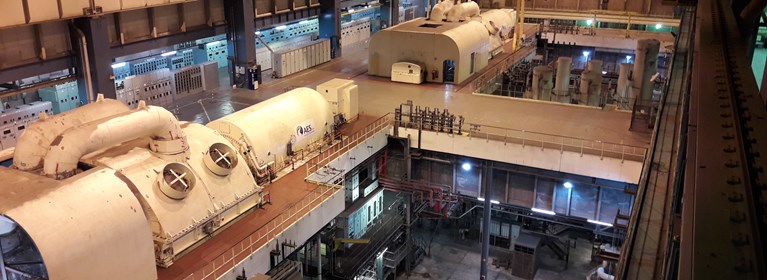
Power and Utilities | Crane Systems | Power & Motion Technology | Automation | By Samantha Lotz | 31 Jul 2018
Producing nearly one-third of Northern Ireland’s electricity, a coal-fired power station had been reliant on a crane control system that operated using expensive, unreliable contactor controls from the 1970s comprised of older, difficult-to-source parts.
The power plant generates electricity from a combination of coal and oil-fueled generators, along with additional gas turbines. Two overhead traveling cranes operators in tandem to move and maintain 100+ ton power generating turbines.
Historically, the power plant experienced excessive crane downtime due to lack of availability of replacement contactor controls. Additionally, the contactors offered limited control and unstable crane movement.
The power plant owner offered a challenge: how can the system run more efficiently, reduce lifetime maintenance costs, and achieve increased reliability, performance, and control? The answer: Magnetek, the one-stop source for material handling control solutions.
Magnetek was able to provide an entire control system, which optimized craneperformance and minimized sourcing logistics. Magnetek worked with the Northern Ireland office of its parent company, Columbus McKinnon, to conduct live demonstrations of feature-rich IMPULSE® Series 4 drives and radio remote control products. Other competitive solutions could not match Magnetek’s best-in-class system or application expertise. IMPULSE drives’ crane and hoist specific software surpasses the performance and safety capabilities of generalpurpose drives and, unlike general-purpose drives, meet the heavy-duty ratings required for this type of application and offer a significantly longer average time between failures.
Columbus McKinnon in Northern Ireland retrofitted Magnetek’s control solution on the power station’s turbine crane. IMPULSE drives improved control with more precise lifting, reliable operation, operator feedback, and the ability to adjust crane functionality, which was not available in the original controls. With IMPULSE® drives’ custom software, load swing was significantly reduced, which enhanced operator safety and decreased stresses on structural, mechanical, and control components.Communication among the radio remote control system components, comprised of the MLTX2™ radio remote control, Flex M wireless receiver, and Radio Drive Serial Interface (RDSI), and the IMPULSE drives allowed the power plant to better schedule maintenance and avoid lengthy downtimes.
Magnetek’s MLTX2 replaced wired pendants, which enabled freedom of movement for operators within the plant. Lightweight and reliable, the MLTX2 radio remote control incorporates the latest electronic technology in a super-tough housing made to withstand harsh environments. MLTX2 includes a graphic display to keep operators informed of system status at all times, and makes configuring access codes, channels, and other system settings simple.
The versatile Flex M features a modular plug-and-play design that allows one plant to use the same type of receiver component for any size application. Flex M provides digital, analog, and serial interfaces, and can manage systems from simple relay outputs to complex I/O and communication networks.
RDSI enables two-way communication between the MLTX2 and IMPULSE•G+ and VG+ Series 4 Adjustable Frequency Drives. While RDSI commands the drive, the operator monitors performance parameters directly on the transmitter’s display screen to better understand faults from the floor.
As the project was completed and expectations were met and surpassed, the owner’s only remaining question was, “Why didn’t we upgrade to Magnetek controls sooner?”
Magnetek eliminated downtime due to difficult-to-acquire replacement controls and enabled precision positioning control for our customer. By doing so, we reduced reliance on aging and unreliable contractor systems. We were also able to complete system upgrade within timeframe of plant shutdown.
Magnetek provided the entire material handling crane control system with 24/7/365 support, while implementing easy-to-use two-way communication system with feedback. We also utilized Magnetek’s VFD control technology, rather than outdated contactor controls and coordinated with Columbus McKinnon office in Northern Ireland to install system.
Access the Full Case Study

Related Articles
Shipbuilding System Upgrade
Newport News, VA
As the largest shipbuilding company in the United States, Newport News Shipbuilding needs to be at the top of their game to effectively build the most advanced ships in the world. By modernizing crane control systems on a pre-determined schedule, NNS avoids lengthy downtime and critical operation issues. That's where Magnetek comes in.