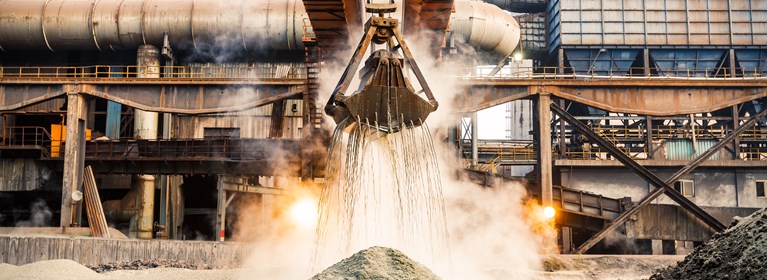
Metals Production | Manufacturing | Crane Systems | Power & Motion Technology | By | 23 Sep 2020
PRODUCTS AND SERVICES:
- IMPULSE®•G+/VG+ Series 4 Variable Frequency Drives
- IMPULSE®•Link Software with Wireless Access
- Advanced Bucket Control Custom Software
- Dynamic Braking Resistors
- Programmable Logic Controller (PLC)
- Human Machine Interface (HMI)
- Automation Division Services
Challenge
- Develop an automated solution to replace manually operated controls
- Enable consistent cleaning schedule for scale pit clarifier
- Reduce reliance on manual controls
- Provide a more effective process to filter mill scale from water
Solution
- Installed fully automated solution limiting human involvement in hazardous areas
- Enabled consistent, accurate movement for efficient scale pit cleaning
- Integrated wireless communication for continuous system analytics and diagnostics
- Improved safety, uptime, and productivity with crane-specific specialty software
A steelmaking facility found their mill scale clarifier to be inefficient, occasionally causing equipment damage and interruptions to the production process. Mill scale is a by-product of water jets cooling steel. A clarifier crane system separates mill scale from the water, collects it into piles, and removes the product for resale. Then, the remaining water is treated and rerouted for processes inside the steel mill. The system needed to be upgraded to keep this process running smoothly.
The original crane system utilized outdated contactor controls and was manually operated by technicians, which pulled them away from their main duties. Due to lack of system monitoring, the accumulated piles of scale overflowed in the outdoor area and interfered with crane movement. Buildup from scale in the recycled water also clogged spray nozzles within the steel plant and caused costly, time consuming maintenance.
The automation team was able to design an innovative automated solution to improve the steel plant’s safety, uptime, and productivity The new system included complete control panels, Magnetek® brand IMPULSE®G+ and VG+ Series 4 Variable Frequency Drives with custom, crane-specific software, dynamic braking resistors, and integrated a programmable logic controller (PLC) and PC-based human machine interface (HMI), all of which were connected via Ethernet communication to report analytics and diagnostic information.
Programmed to initiate automatic cycles at specified times, the new scale pit clarifier system was designed to complete safety checks and ensure all parameters are met before operation begins. If any parameters are not met, a technician is able to access the HMI that displays information from the system to determine which parameter is preventing operation. The HMI, as well as additional computers and monitoring equipment, are located in an off-crane control room, providing a center of operation for technicians and enabling remote access when needed. IMPULSE®•Link software, which enables easy programming, monitoring, and troubleshooting for multiple variable frequency drives, helps ensure the crane stays up and running by displaying analytics and diagnostic information on the HMI in the control room.
Once safety checks are complete, the clarifier crane leaves its parked position and moves to the designated mill scale reservoir. To determine the cleaning sequence, the hoist encoder measures the height of the scale piles at each pick point and returns to the highest point once all of the pick points have been measured and recorded, omitting any point that is already below the clean depth set point. The hoist, controlled by Magnetek-brand IMPULSE•VG+ Series 4 Drives, lowers a bucket into the scale pit until a slack cable condition is detected. The IMPULSE drives’ Hook Height Measurement feature uses an incremental encoder signal to determine hook height from a calibrated position. Built-in Bucket Control Software in each drive controls the various bucket motions and provides operators with the open/close status of the bucket, even when underwater.
The trolley and bridge motions, controlled by Magnetek-brand IMPULSE•G+ Series 4 Drives, use absolute encoders for positioning, making it easy to move the scale to the dump area for collection and removal. The computer-controlled system monitors the scale deposits in the dump area so the crane can automatically select a dump location, selecting a different location each time in order to minimize the amount of scale at each location. Piles are collected in more consistent and manageable sizes, which helps minimize obstructions for the crane and ensures easy disposal.
Integrated with the IMPULSE drives, Ethernet communication requires less wiring in the system, allows for remote access to adjust parameters, and simplifies programming of the PLCs. To assist with commissioning, engineers accessed the wireless system remotely from the Magnetek facility in Menomonee Falls, WI, to adjust software to fit exact operation needs.
Today, the customer’s fully automated mill scale clarifying system operates without any human interaction. The recycled water used in plant processes is cleaner and requires less treatment. Cleaner water also results in fewer plant equipment repairs. In addition, technicians can more efficiently complete their main responsibilities, leaving automation technology to control the clarifier system. Relocating the monitoring equipment off-crane has created a much safer work environment and with continuous analytics and diagnostics, operators can stay more informed of system status, helping to plan equipment maintenance. Together, all of these improvements have created a safer and more efficient steel mill for the customer.
Automated Scale Pit Crane System
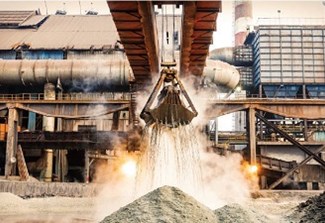