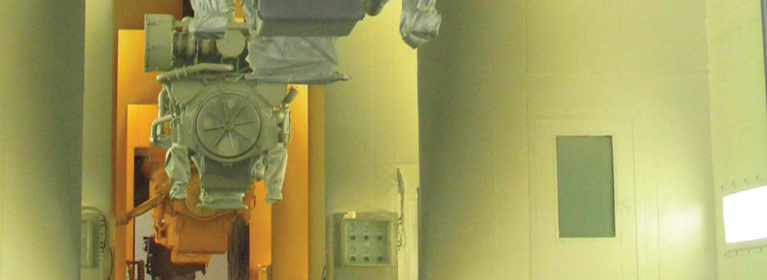
Automotive Industry | Manufacturing | Crane Systems | Power & Motion Technology | Automation | By Lynn Bostrom | 17 Sep 2009
The newest and largest diesel engines Caterpillar has ever produced, the 3500 and 3600 Series, are manufactured at their facility in Lafayette, Indiana.
The engines cover a horsepower range from 600 to 7300 and weigh up to 34,000 pounds. In preparation for their production, Caterpillar initiated a program to transform their manufacturing systems to set new standards for quality, safety and speed in the industry.
Improving manufacturing flexibility and providing additional production capacity were the goals of the production line initiative at the Lafayette facility. One of the improvement projects was to create an automated paint line monorail system that could handle the size and weight of their new engines.
Magnetek’s Engineered Systems Group designed an automated paint line monorail system which eliminates idle time, rework and excess inventory. The facility can now paint these new engines in the safest, most reliable and fastest way possible. The old paint line was completely removed and the new system was put into place with 13 carriers running through wash, dry, paint and cure stations. To facilitate a smooth, effi cient and safe workfl ow, an RF communication network between the fl oor equipment and each of the carriers was installed.
Build an automated paint line to handle a new series of larger 34,000-pound engines while expanding production capacity from under 50 engines painted per day to a goal of over 70 engines per day.
Magnetek engineered a customized system that increased efficiency and manufacturing flexibility, expanded production capacity and reduced lead times for the end user.
Access the Full Case Study
Magnetek designed an automated piant line monorail system which eliminates idle time, rework, and excess inventory. The facility can now paint engines in the safest, most reliable, and fastest way possible.
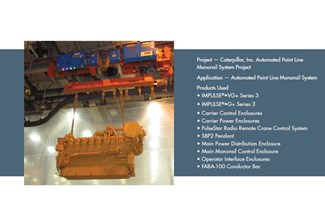
Related Articles
Automated Wheel and Strut Paint Line Monorail System
US Air Force
The United States Air Force Base's aircraft maintenance group worked with Magnetek to design a customized overhead materials delivery system that automated and integrated nine overhead monorail carriers that automated and streamlined the wheel and strut paint line process.