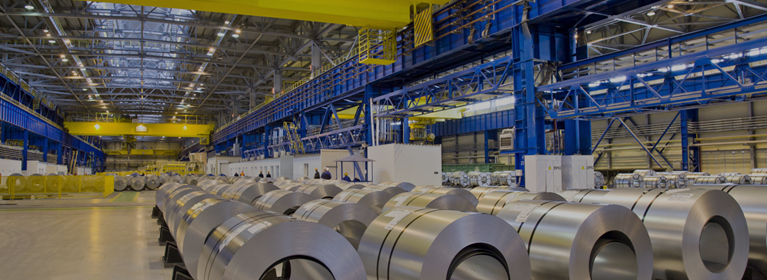
The Challenges of Implementing Crane Automation
Automation | Power & Motion Technology | By Rick Emmer | Jun 25, 2021
Implementing automation in your facility can significantly impact the safety, uptime, and productivity of your systems and processes. Deciding where to integrate automation, determining the return on investment (ROI), and being prepared to support and maintain automated systems once they are in place can seem daunting.
In this blog, we’ll talk about some of the most common challenges to implementing automation and what you can do to address them.
Contact our Automation Team to Discuss Your Application Today
Challenge #1: Deciding Which Processes to Automate
There can be multiple processes and systems needed to get the job done in any facility. Deciding which processes to automate can be tricky. The first two questions you should ask yourself are, “What are the most important processes to our business?” and “What are our most high-value processes?”
Automating the most critical processes in your facility is a great place to start. By automating key processes, you can ensure that they stay up and running efficiently. This increases uptime and, ultimately, improves the productivity of that process. And, by automating key processes, you are in a better position to scale operations to grow the business.
The other important thing to keep in mind is that automation doesn’t have to be complicated. Integrating a few automated solutions into your system can go a long way to create a safer, more streamlined process. Start small, and, once you experience the benefits automation can provide, you can build on that automation framework to further improve operations.
Challenge #2: Fear of Replacing People with Machines
When people hear “automation,” a common assumption is that automation technology will replace personnel. This doesn’t have to be the case. While automation may replace specific jobs or positions within a process, it does not need to eliminate the people themselves. Automation gives you the ability to redeploy personnel to different tasks or operate other machines. With automation increasing throughput, employees can work on steps further along in the process to keep increased production running smoothly.
Automation can also be used strategically to remove personnel from dangerous or high-risk process areas or those that pose ergonomic challenges. For example, if you’re transporting molten metal or moving a heavy object repeatedly, automation can help keep your employees safe and reduce fatigue. Then, they can be redeployed to other areas within the facility to increase production where needed.
Challenge #3: Determining Return on Investment
One of the biggest roadblocks to implementing automation is determining ROI by balancing the upfront cost of the automated solution with the long-term benefits and cost savings it will provide. First, you should understand the need for automation and show the value in that. Do you need to reduce downtime? Increase production? Prevent injuries?
Here are a few key things to look at when calculating ROI:
- To what degree will productivity and operational efficiencies be increased? How many more products/items per hour can you produce?
- Will this technology help reduce injuries? What are the costs associated with those types of injuries?
- What type of labor savings can be realized for your process? Where can personnel be redeployed because of automation technology, and are there any cost or production benefits?
- What can I expect in terms of reduced equipment maintenance? How much does downtime for maintenance cost, and how much will automation technology minimize downtime?
By calculating these potential cost savings and benefits, you’ll be in a better position to “sell” the need for automation technology in your facility. In addition, ROI helps demonstrate the “why” behind the technology and shows the tangible benefits the technology can provide long term.
Challenge #4: Supporting, Managing, and Troubleshooting the System Long Term
Automation technology can be complicated, but managing, supporting, and troubleshooting it shouldn’t be. By working with an automation expert, you’ll gain a detailed understanding of how your automated solution works, so you’re able to support the system during normal operation. If the system and technology are user-friendly, managing breakdowns, maintenance, and technical support should be easy and intuitive. Remote connectivity, for example, makes it easy to monitor your system, troubleshoot issues, and adjust parameters as changing crane, process, and plant conditions require.
Look for an automation provider with a deep understanding of the technology and how it can be customized and simplified for your exact application needs. In addition, they should work with you every step of the way, from quotation to commissioning and training, so you understand how the system works and are prepared to manage it long after the installation is complete.
To learn more about how automation technology can improve your facility and operations or speak with one of our automation specialists, contact us today!
START A CONVERSATION WITH OUR AUTOMATION DIVISION
Rick Emmer
Rick Emmer is a Business Development Manager for Columbus McKinnon's Automation Division. Rick has over 25 years of experience and a deep understanding of how to deliver the right automation solution to best meet customers' application needs in the conveyor and palletizing industries. Rick holds a BS Degree in Business with a Major in Marketing from the University of Wisconsin - Milwaukee.
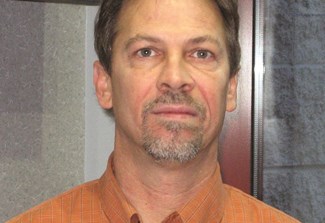
Our automated crane systems are designed to improve safety, uptime and productivity in your facility. Not only does crane automation technology allow you to build safety right into equipment with no-fly zones and off-center pick prevention, it also provides you with real-time data and information that enables you to improve operational efficiency and make smarter decisions, faster.
Columbus McKinnon’s Unified and Magnetek brands bring more than 20 years of experience in delivering automated systems to the automotive industry. Our high-technology solutions are featured throughout the automotive manufacturing process, including ergonomic and autonomous workstations like ProPath™ and Intelli-Guide™.
Automated Systems
At Columbus McKinnon, we are dedicated to accelerating innovation and expanding our portfolio of automation and diagnostic solutions. One way we are doing this is through the development of intelligent automation solutions for new and existing cranes. See how our technology is helping to create the smart cranes of the future.
Related Articles
Three Ways Automation Technology Can Improve Your Facility & Operations
Implementing automation in your systems and processes can have a big impact on your facility. Let’s take a closer look at three ways automation can improve your facility and operations.
Do you have technology in place to help you plan maintenance to prevent costly downtime? Do your processes suffer from complexity that causes variations in product quality? Let's take a closer look at three ways automation can improve your facility and operations.
One form of crane automation technology that can have a big impact on your facility and operations is an auto-dispatch system. How can this help? Combining radios, drives, motors, brakes, and automation programming, auto-dispatch systems allow operators to automatically send a load to pre-programmed areas in a facility with the push of a button. They no longer need to manually guide or follow the load to the next location in the process. Learn more about all of the benefits.
Incorporating Smart Solutions into the Steelmaking Process
From steel production to distribution, innovative technology helps increase your safety, uptime, and productivity.
The demand to incorporate smart solutions and automation throughout every step of the steelmaking process is rapidly increasing. Columbus McKinnon offers products that assist from steel production to distribution, utilizing innovative technology that helps increase your safety, uptime, and productivity.