Automotive Automation Systems
Columbus McKinnon’s Unified and Magnetek brands have more than 20 years of experience delivering automated systems to the automotive industry.
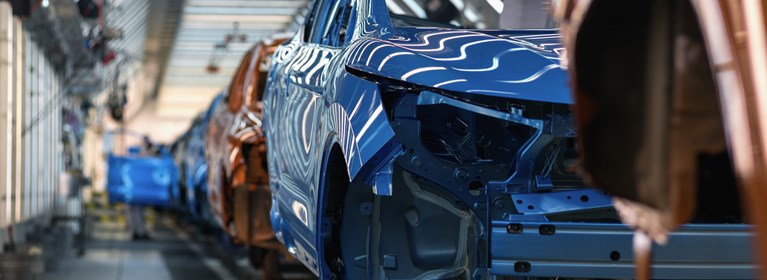
Automotive Factory Automation from Start to Finish
From the first step of the automobile production process to taking the final assembled vehicle off the line, automation technology is hard at work. Time is money, so productivity is critical and uptime is of the utmost importance.
For this reason, optimization of the automotive assembly line has always been an essential element within any automobile manufacturing facility and automation can help. In 1954, General Motors introduced Unimate, the first industrial robot, and is one of the largest users of robotic automation among U.S. automakers. And, that was only the beginning. Automotive automation technology continues to evolve, helping manufacturers meet the needs for increased productivity.
So, what is automotive automation?
Simply put, automotive automation is the use of computer-programmed mechanical equipment during the assembly of an automobile. Automotive automation technology ranges from a pre-programmed overhead crane repeatedly delivering transmissions to a set location in a facility to robotic arms installing windshields without the need for human assistance. Not only does this technology reduce takt time, it reduces the chance of human error and accidents.
Automated Car Manufacturing Systems from Columbus McKinnon
Columbus McKinnon’s Unified and Magnetek brands have more than 20 years of experience delivering automated systems to the automotive industry. Our primary solutions are featured throughout the automotive manufacturing process include ergonomic and autonomous workstations like ProPath and Intelli-Guide™.
- Body-in-White (BIW)
During the BIW stage, the non-painted steel frame of a vehicle is assembled. The frame of the vehicle is delivered to a precise location on the assembly line and robotic arms or workers are tasked with welding, riveting, clinching, bonding, or laser brazing to complete the assembly. - Body Shop
The vehicle skeleton is assembled in the BIW stage, but the external-facing pieces, such as the roof, side panels, doors, hood, truck, bumpers, and more, are assembled in this phase. Rather than fetching all these components one by one, an auto-dispatch system is used to automatically retrieve the items, allowing the assembly worker to simultaneously secure the previous item to significantly reduce takt time.
- Paint
Vehicles are painted using an electro-static process. This process involves electrically charging the paint and the materials to be painted with opposite charges. Since opposite charges attract, paint only adheres to the intended products. The voltage necessary in this process can be as high as 700 VDC so it’s best to clear the area of all personnel and automate this process. - Final Trim & Chassis
During this stage, everything from the HVAC system and seats to the radio and dashboard are assembled. Once the interior trim has been assembled it is married to the chassis.
- Powertrain
While all the above is happening, the powertrain is being assembled in a different area of the facility. The engine and transmission are assembled, torque tightening, torque damping and gap setting are all completed. This is a crucial step in the process and one where automotive automation plays a major role. Using our automation technology, we helped an automotive manufacturer reduce the takt time during the engine and transmission assembly process from 58 seconds to 22 seconds.
Whether you’re looking to reduce takt time or improve safety and quality along the assembly line, integrating automation systems in the automotive manufacturing process can deliver an immediate and long-term impact. Take the first step to finding the right automation solution for your facility by starting a conversation with one of our automotive automation specialists today.
START A CONVERSATION WITH OUR AUTOMOTIVE DIVISION