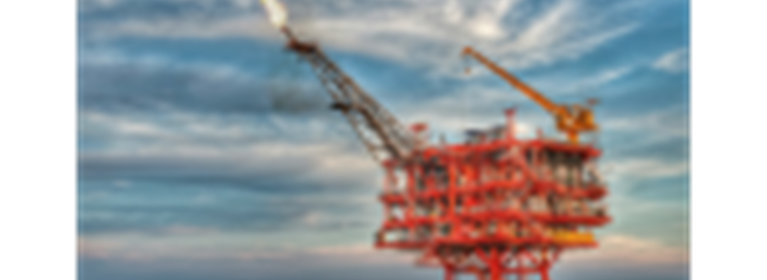
Using Cranes and Hoists in Hazardous Areas
A Guide to Spark Resistant and Explosion Proof Lifting
Mining, Petroleum and Gas | Crane Systems | Hoisting & Lifting | Safety and Training | How To's | by | 25 May 2020
The Need for Spark Resistance Lifting Equipment
Across a variety of industries, ranging from upstream oil and gas and refining to agriculture and woodworking, potentially flammable atmospheres can present a unique set of challenges for material handling equipment. These environments can pose a serious threat to materials, equipment, and, most importantly, personnel.
In the U.S., NFPA 70, part of the National Electric Code (NEC), addresses the design and installation of electrical conductors and equipment in hazardous areas but does not specifically provide guidelines for mechanical equipment used in these same hazardous locations.
Download a free guide to lifting in hazardous environments.
The Importance of Spark Resistance
The NEC breaks down hazardous areas into different types of explosive atmospheres, two of which are those involving flammable gases and those involving dusts. These hazard Classes are further clarified by Group and Division.
Hazardous Atmosphere Category (Gas or Dust Grouping) |
||||
---|---|---|---|---|
Explosive Atmosphere | Typical Hazard Material | North America NEC Hazard Catagory | 500-503 / cec 18 Grouping | NEC 505 / CEC 18 Gas Grouping |
Gasses and Vapors |
Acetylene |
Class I |
Group A |
ICC |
Dusts | Metal Dust Coal Dust Grain Dust |
Class II | Group E Group F Group G |
— — — |
Fibres and Flyings | Wood Paper Cotton |
Class III | — | — |
It is generally understood that friction between certain materials can cause sparks sufficient enough to ignite flammable gas or dust. A cigarette lighter or an antique flintlock musket are familiar examples of this. Obviously the type and concentration/dilution of gases in an area is one element that affects potential ignition from a mechanically generated source, but other key factors could include:
- The type of materials making contact
- The speed/pressure with which the materials come into contact
- Corrosion on one or more of the contacting surfaces
- Lubrication
Contact between steel surfaces can create sparks as well. Steel is commonly used in most hoists and cranes for load-bearing components such as hooks, lower blocks, load chain, and trolley wheels. This renders most lifting equipment unsuitable for certain hazardous environments.
To address this potential risk, choose material handling products built with materials such as copper, bronze, and austenitic stainless steel, which are generally considered non-sparking, for coatings or as material substitutions for enhanced spark resistance. Not only are these materials spark resistant, but they protect against corrosion. Since surface corrosion can increase friction between mating components, corrosion prevention is vital when lifting in hazardous environments.
Select lifting and hoisting products with spark-resistant components and finishes, including:
- Solid bronze hooks, bottom blocks, and trolley wheels
- Bronze plated components
- Stainless steel load and hand chain
- Multi-coat epoxy finishes
- Zinc-aluminum corrosion-resistant finish
The Need for Corrosion Resistance
It is vital that lifting equipment used in classified hazardous locations must be compliant with NEC, IEC, or other applicable standards. Care should also be taken to ensure mechanical spark resistance for critical components, such as load blocks, hooks, trolley wheels, load brake, and lifting mediums like chain and wire rope, in these locations. In addition to spark resistance, corrosion protection for lifting equipment is equally important in these environments to ensure the safety of personnel, equipment, and the facility itself.
Many classified hazardous areas exist outdoors, exposing lifting equipment to direct and often harsh weather. This includes applications such as offshore oil platforms, natural gas processing plants, and refineries – to name a few. Specifically in offshore facilities, equipment may be exposed to splash zones, salt spray, and the condensation of salt-laden air. In addition to harsh and corrosive weather conditions, sulfur, mineral acids, and other corrosive agents are often present in the crude oil and natural gas that is being produced, processed, and transported in these facilities, working to further corrode lifting equipment used in these environments.
The total cost of corrosion can be tremendous, adding up to billions of dollars each year in the oil and gas industry alone. For these companies, the cost of repairing and replacing corroded lifting equipment paired with unscheduled maintenance, downtime, and lost production can have a major impact on their profitability. In addition, corroded load blocks, hooks, chains, and cables can result in catastrophic equipment failure. Not only can this cause costly damage to equipment and the facility, but most importantly, it can injure or even kill operators and other individuals in the facility.
So how do you protect lifting equipment from corrosion?
The use of corrosion-resistant materials for load blocks, hooks, chains, cables and other components is critical. And, since surface corrosion can increase the friction between mating components, corrosion prevention can also be important in maintaining mechanical spark resistance when using these products in classified hazardous environments.
Always look for lifting solutions with spark and corrosion-resistant materials and coatings. Meet with a lifting application engineer to determine what solution would best suit your application and to see if a custom solution is necessary.
Corrosion-Resistant Features Include:
- Solid bronze hooks, bottom blocks, and trolley wheels
- Lightweight aluminum housings
- Stainless steel load and hand chain
- Multi-coat epoxy finishes
- Zinc-aluminum corrosion-resistant finish
Download a free guide to lifting in hazardous environments.
In addition to corrosion-resistant materials and finishes, ensure proper hoist lubrication to prevent sparking. These measures, combined with a robust inspection and preventative maintenance program that includes pre-lift inspections, play a critical role in ensuring the dependability and safe operation of lifting equipment in these harsh environments.
Space Constraint Challenges
Classified hazardous areas frequently exist within confined spaces, especially in the mining and oil & gas industries. In mining, tunnels often have low overhead clearance in areas where coal or other flammable dust may be present. In the oil and gas industry, designers of offshore facilities typically look to minimize the overall size of the structure, which can lead to low headroom between deck levels and tight clearances for monorails and crane runways.
In all of these situations, there is a need for overhead lifting equipment that is compact in design, including low headroom and short side clearances, as well as a short “end approach” to maximize the deck coverage area served by the monorail hoist or crane.
This need for compact hoists, trolleys, and cranes is often complicated by the possibility that flammable gases or dust may be present in the areas where the equipment is used. Explosion-proof and spark-resistant features may be needed, each posing their own challenges given the space constraints. See the Yale ATEX 360 hand chain hoist.
Explosion-proof electric motors and control enclosures are typically larger and heavier than those for non-hazardous areas. Spark-resistant bronze load blocks and hooks tend to be larger than carbon or alloy steel hooks and blocks with the same safe working load. The use of spark-resistant stainless steel load chain or wire rope often requires the equipment capacity to be de-rated due to lower tensile strength of stainless versus alloy steel. This de-rating can sometimes result in larger, heavier and more costly hoists and cranes. Always consult an application specialist and ensure operators are thoroughly trained in hazardous lifting applications.
![]() |
![]() |
Lifting Solutions for Hazardous Environments with Space Limitations
There are many factors to consider when specifying or purchasing lifting equipment for hazardous locations with space limitations. When environmental dimensional constraints compete with the need to comply with hazardous area requirements, the safety of personnel, equipment, and facilities themselves must always take precedence in your decision making.
Fortunately, there are a variety of equipment options available, featuring spark- and corrosion-resistant materials and explosion-proof components, that can be used in confined areas. Low-headroom hoists are offered in both wire rope and chain varieties, including manual, electric and pneumatic models.
Wire rope hoists can typically provide higher capacities and faster lifting speeds, while chain hoists can offer smaller overall dimensional envelopes to optimize end approach and clearance. Solid bronze and stainless steel components can provide lasting protection against sparking and corrosion, but, in some applications, copper or nickel plating can be substituted to provide lower headroom dimensions and reduce the need for de-rating of safe working loads.
Columbus McKinnon provides solutions for the most challenging applications in hazardous environments. The Yale ATEX 360 hand chain hoist allows for operation at any angle, including above the load. Chester Hoist is best known for ultra-low headroom hoists and custom design. The industry-leading, low-profile designs and rugged durability of Chester hoists make them ideal for harsh marine environments and confined spaces between decks on ships and offshore oil facilities. STAHL CraneSystems is known worldwide for its comprehensive portfolio of explosion-proof lifting, drive and control technology.
Columbus McKinnon offers an extensive range of additional services ranging from consulting and engineering to country-specific management of approval and certification procedures, for explosion-proof and hazardous environment applications.
Download a free guide to lifting in hazardous environments.
Regardless of your industry or where you do business, Columbus McKinnon has the hoists, cranes and application expertise to keep your people, materials and equipment safe in classified hazardous and corrosive environments.
Related Articles
Proper selection and specification of hoists, cranes and rigging hardware is always essential to safe overhead lifting, but in no environment is this more critical than on offshore oil and gas facilities.
For natural gas filter towers in the Saudi-Arabian desert, our Pfaff Silberblau team in Germany, has developed and installed a special lifting and traversing system for changing filter elements.
Two prime causes of accidents are overloading and poor rigging. To prevent accidents, we suggest these guidelines: