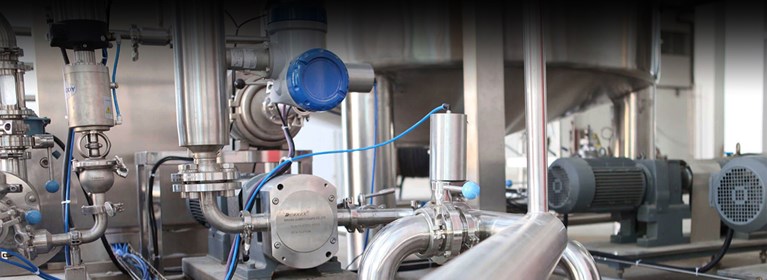
Dissecting the Growth of the Linear Motion Market and the Skills Gap
Manufacturing | Industry News | By Duff-Norton | Oct 22, 2019
By 2021, the market value of the global linear motion systems industry is expected to reach $7.94 billion (US). With a compound annual growth rate of up to seven percent between 2017 and 2021, the main cause for the expansion of the linear motion industry is the constant demand for larger quantity, higher quality products.
From a manufacturing point of view, consistent use of linear motion products, such as linear actuators and screw jacks, causes them to wear down and require replacement. However, this is only one aspect of the bigger picture. There is a significant skills gap in the US manufacturing industry that is causing many companies to weigh up the value of automation against the traditional labor force to meet this growing demand.
The growing skills gap
The talent shortage in US manufacturing is exacerbated by three key issues: the retirement of ‘baby boomers’, economic expansion, and a lack of qualified graduates.
Baby boomer retirement
We have reached the time when the workforce born between 1946 and 1964, the ‘baby boomers’ as they are known, are now beginning to retire. In the manufacturing industry alone, an estimated 2.7 million jobs will need to be filled when the current workforce retires.
Almost three-quarters of executives feel that the retirement of engineers and skilled production workers will have a significant or high contribution to the future talent shortage.
Economic growth
As the industry expands, it is natural for more jobs to become available and it’s estimated that general economic growth will open up 700,000 jobs in the manufacturing industry. This figure is on top of the resources gap left by the baby boomers.
Industrial machinery mechanics, computer-controlled machine tool operators, and machinists are the top three manufacturing occupations projected to be the most heavily required jobs over the next four years.
Graduate skills shortage
Naturally, as older generations retire, and more jobs become available, there is a stronger need for more talented graduates to fill the positions. However, the future talent pool will have significant skill deficiencies that are concerning manufacturing executives:
- More than 50 percent of executives believe the future talent pool lack will lack problem solving skills;
- 43 percent say there is a lack of basic technical training;
- 66 percent believe there is a significant lack of workers with technology/computer and mathematical skills.
What does this mean for the industry?
The three workforce segments with the greatest hiring challenges will be skilled production, production support, and scientists and design engineers. With that in mind, if manufacturing companies are to capitalize on the growth of the linear motion systems market, then they need to combat the growing skills gap. They can do this by:
- Championing STEM subjects in schools. In 2016, the US had an average of 568,000 recent STEM graduates, placing it third in the world behind China (4.7m) and India (2.6m). Combating the skills gap starts with companies in need of STEM graduates championing the teaching of these subjects in schools and colleges.
- Partnering with local colleges. Nurturing home-grown talent should be a number one priority for manufacturers. By partnering with local colleges and vocational schools, they can provide much needed industry insight and support to the younger generations and foster a new generation of engineers and machine specialists.
- Offering skilled labor apprenticeships. Apprenticeships are an invaluable resource for employers but too few Americans are taking advantage of them. ‘Even though about 150,000 Americans start an apprenticeship each year,’ says Mark Mills, faculty fellow at Northwestern University’s McCormick School of Engineering and Applied Science, ‘the total would be one million to three million a year if as many US millennials signed up as they do per capita in France, Germany, England and Switzerland.’
The next five years promise to be exciting for the linear motion industry, but companies have work to do today to ensure they have a competent workforce to reap the rewards of this exponential growth tomorrow.
What are your thoughts on how the growth of the linear motion market is creating a skills gap? And what can manufacturing companies do to close the gap?