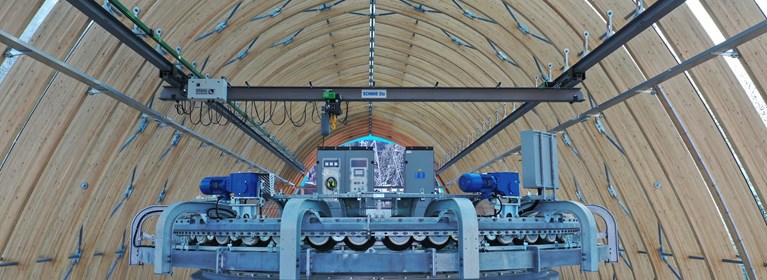
Symbiosis of wood and steel - New crane systems for the Nebelhornbahn (Nebelhorn Cable Railway)
Metals Production | Manufacturing | Crane Systems | Hoisting & Lifting Equipment | By STAHL CraneSystems | Jan 18, 2022
This isn’t the sort of project you get every day, particularly when it concerns the location of solutions. Hubert Schmid Bauunternehmen, crane construction partners of STAHL CraneSystems, received the order for the design and assembly of a total of four crane systems, which are intended for maintenance work in the stations of the Nebelhornbahn in the Allgäu Alps. Next to the time, logistical, and construction-related challenges, architectural features had to be considered.
The Nebelhorn belongs to the Daumen Group of the Allgäu Alps. Tourists can reach the 2224-metre mountain on foot, or much faster and more comfortably with the Nebelhornbahn. It started its maiden voyage in June 1930 and is still one of the longest passenger overhead railways in the world.
Starting in 2019, over 90 years later, the Nebelhornbahn was completely modernised, making room for a new 10-seater gondola lift that takes visitors up to the summit.
With a total investment of around 55 million Euros, Oberstdorf-Kleinwalsertal mountain railways made extensive use of environmentally friendly and ecological construction methods in the project.
Cable car technology from the expert
Construction work on the Nebelhorn in Oberstdorf began in summer 2019. A variety of modernisation measures included a new valley and middle station and the expansion of the mountain station. In addition to barrier-free access, comfort is top priority for visitors. Each passenger should have a seat to enjoy the view. And there is no need to change the gondola at the middle station, which shortens waiting times on the way to the summit.
The entire cable car technology, including controls and cabins, was delivered by Leitner AG based in Sterzing, South Tyrol. “We basically deal with all aspects of cable car technology systems worldwide. As the overall project planner for the Nebelhornbahn, we also took on responsibility for the mechanical assembly and electrical installations,” reported Gerald Senn, construction site manager for cable car technology at Leitner.
“With regard to the crane technology for the individual stations, the systems had to be partly built into areas with very limited space and also adapted to pre-existing building conditions and peculiarities. In the end, we appointed Huber Schmid as partner for the project, because the company not only had the knowledge to implement the crane technology we wanted, but also offered solutions for the occasionally special interfaces that had to be considered here. As a regional company, Hubert Schmid can also ensure a reliably local service for crane systems,” said Jan Sorg, Project Engineer at Leitner.
For Hubert Schmid, the project started in mid-2020, whereby the assembly times of the cranes were based on the construction progress of the individual railway stations. “So on average, we only had a few days for assembly and installation. Therefore, among other things, we pre-assembled the cranes in the factory,” explained Rainer Haase, Project Manager at Hubert Schmid Bauunternehmen GmbH.
A lot of precision work, not only during transportation
The mountain station of the Nebelhornbahn, which is 1932 m above sea level, proved to be a real logistical challenge, because the cranes and components had to be transported to the operation site over narrow, steep mountain roads using the great skill and experience of the lorry drivers. “And we also reloaded our assembly materials and tools into all-wheel drive vehicles to reach the mountain station,” said Rainer Haase.
From Gerald Senn’s point of view, there were also challenges when installing the cranes themselves. The roof construction of the mountain station consists of laminated wooden beams. The monorail suspension crane with a load capacity of 1.6 tons had to be installed horizontally suspended when the roof was sloping. “The running track of the crane was therefore mounted on the stepped-like arrangement of laminated beams. Each individual suspension of the monorail is therefore a special construction,” stated Senn.
Chain box according to customer wishes
The length of the crane's monorail (maximum travel speed 40 m/min) is 13.42 m. A hoist with an ST 30 chain hoist, a lifting height of 8.5 m, a lifting speed of max. 8 m/min and a maximum cross travel speed of 20 m/min was also installed. The chain hoist featured a special chain box at the customer’s request. Rainer Haase explained “In spaces with high interfering edges, the chain box sometimes hangs lower than the crane hook. Since cable car technology has many moving parts, a safety distance of at least 500 mm must be maintained at all times. Therefore, a shortened chain box made of sheet steel was chosen for the chain hoist.”
When every millimetre counts
Two cranes were installed at the middle station, one of which was a single-girder suspension crane with a load capacity of 2 tons and a maximum speed of 20 m/min. This crane, with a crane track length of 28.92 m, was also attached to the laminated beams. In connection with this, it was necessary to take the longitudinal expansion of the laminated beams into account due to temperature fluctuations when connecting the beams for a smooth running of the rollers.
Since all maintenance areas should be easily accessible with the hoist (max. lifting height 19 m) within the restricted height of the middle station, the available space in height was particularly significant here. For this reason, an STK 50 chain hoist with extra-short headroom trolley and integrated special chain box was used.
With a height reduced by 60 %, the extra-short headroom trolley achieves a maximum hook path, which is particularly advantageous in confined spaces such as the middle station. The distance from the lower edge of the carrier to the base of the hook is merely 210 mm or even just 185 mm depending on the load capacity of a crane. The vertically mounted chain hoists used here are based on the standard components of the ST chain hoist program of STAHL CraneSystems. The patented chain guide is unique, with two separate, synchronously running chains acting on a hook block.
The middle station also has a maintenance section for the cable car gondolas, which has been equipped with a single-girder overhead travelling crane (load capacity 1.6 t, lifting height 8.5 m). Within the restricted height of the maintenance section, the crane must also be mounted as low as possible under the ceiling for maximum low start-up dimensions. “Since every millimetre counts here, we have once again chosen an STK 50 chain hoist with an extra-short headroom trolley,” said Haase.
At one with the architecture
The valley station of the Nebelhornbahn welcomes visitors with its particularly impressive architecture of wood and glass, featuring a total of 39 laminated wooden beams that span an entirely glazed hall 10 metres in height. The single-girder suspension crane with a lifting capacity of 2 tons, as well as a lifting height of 8.5 m, and above all the crane track that runs the entire length of the hall of more than 36 m, should be integrated into the building as harmoniously as possible and should in no way detract from the high-quality architecture.
“The Hubert Schmid construction company has also responded to such special requests to create very individual solutions,” emphasised Jan Sorg.
Instead of flat-rolled steels, a special filigree solution was developed for the suspension of the crane track, which involves a larger cross section in the attachment area on the laminated wooden beams and the crane track, while it tapers out in the middle.
“It exists where a lot of material is needed due to static or absorbed forces. Where, however lighter loads and forces are at work, we were able to dispense with wider cross sections. As a result, the crane track suspension fits perfectly into the overall architecture of the valley station. For crane girders and crane track we also chose a colour that came closest to the hot-dip galvanised crane track suspensions,” explained Rainer Haase. With regard to the length of the hall, the longitudinal extension of the crane track girders over the entire crane track had to be taken into account, since the girders heat up more than usual when directly under the glass. However, due to the bevelled carrier joints at the ends, they adapt flexibly to temperature fluctuations, so that the crane rollers pass over them without disturbance.
Starting the season on a positive note
The crane construction project was completed in March 2021 after about 10 months. Just in time for the planned opening date, the Nebelhornbahn was completed and started its summer operation in May 2021.
“We are completely satisfied with Hubert Schmid’s overall performance and results,” said project engineer Jan Sorg happily, and site manager Gerald Senn once again emphasised the close collaboration: “The communication and organisation at the construction sites worked really exceptionally well in mutual coordination during the project period. If there is a similar project, we will be happy to contact the company again.”