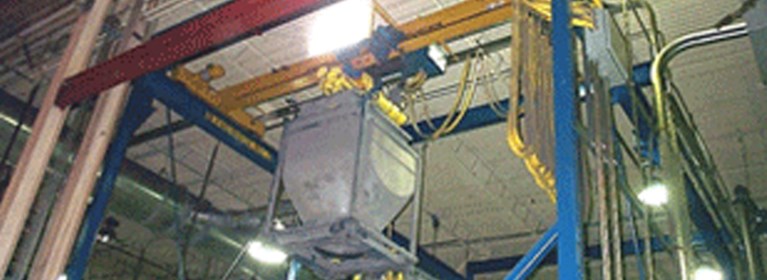
Manufacturing | Automotive Industry | Power & Motion Technology | Crane Systems | By Lynn Bostrom | Nov 05, 2008
As a cost cutting measure, an auto parts manufacturer wanted to reduce the amount of people and space required to manufacture brake pads. The solution entailed creating small work cells within their manufacturing facility. An overhead crane was added to each cell to move hoppers filled with brake pad material to the top of presses that form the brake pads. To help the operator position the load, an auto-dispatch feature was added to the overhead crane control system.
The hoist, bridge, and trolley motions of the overhead crane are controlled by IMPULSE®•G+ drives, while reversing contactors control the grab motion. The hoist is positioned using a 3 position geared limit switch, the bridge is positioned using a laser, and the trolley is positioned using proximity sensors. An Allen-Bradley SLC 5/04 PLC controls the auto-dispatch function and an Allen-Bradley PanelView 1000 provides an operator interface to the system. Position verification sensors are also used to prevent the operator from sending a hopper to an occupied location.
A fork truck brings a full hopper to one of the two entrance areas of the cell. After the fork truck is out of the way, the operator selects the proper entrance location using the PanelView. If the crane determines it is safe, it moves to the entrance location and the grab engages onto the hopper. Once engaged, the operator selects the press location. The system then checks to see if the location is occupied. If not, the crane moves the hopper to the press, disengages from the grab, and stops.
Moving an empty hopper off of a press is done in a similar fashion. The operator selects the press using the PanelView. The crane moves to the location and engages onto the hopper. Once engaged, the operator selects the exit location. If the location is not occupied, the hopper is moved to it, the grab disengages from the hopper, and the crane stops. If a move cannot be performed safely, a message is displayed on the PanelView. Manual control of the crane is accomplished through either the PanelView or a back-up pendant control.
Related Articles
Hurricane Sandy Drawbridge Brakes
New York City, NY
Magnetek restored some of the long-term damage the hurricane caused by refurbishing and rebuilding 16 storm-damaged 300M Mill Duty AC Thruster Shoe Brakes. The industrial AIST rated brakes were fully submerged in saltwater for an extended period following Hurricane Sandy. The rebuilding process returned the brakes to like-new condition, including a new safety orange paint job.
Springtime thaws and flooding along the Red River have been annual problems for the cities of Moorhead, Minnesota and Fargo, North Dakota. To prevent recurring damage to a pedestrian bridge between the two cities and decrease removal and replacement costs, a 168-foot bridge was commissioned with a self-contained lifting system, including new Magnetek radio remote controls and adjustable frequency drives.