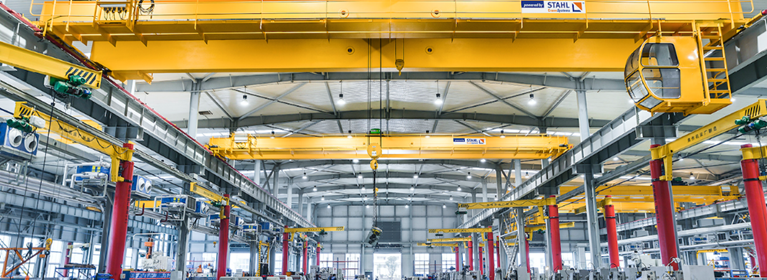
The Benefits of Auto-Dispatch Technology
Automation | By Anthony Alessi | Apr 19, 2021
Does your facility have outdated, manually controlled cranes, hoists, or monorail systems? Converting from manual control to automation technology can bring new life to your equipment, increasing their lifecycles and providing new features to make your operations safer and more efficient.
One form of crane automation technology that can have a big impact on your facility and operations is an auto-dispatch system. How can this help? Combining radios, drives, motors, brakes, and automation programming, auto-dispatch systems allow operators to automatically send a load to pre-programmed areas in a facility with the push of a button – they no longer need to manually guide or follow the load to the next location in the process.
In this blog, we will discuss four benefits of incorporating an auto-dispatch system in your operations.
-
Improved Facility & Operator Safety
Auto-dispatch technology does the work for you by eliminating the need for specialized skills or knowledge of lifting technology, sway control, or protected zones. By setting a crane along a pre-programmed path, you prevent collisions with other equipment or operators for an overall safer workplace. Auto-dispatch technology can also be used to prevent operators from being in unsafe work areas or near dangerous processes, helping to protect them from potential hazards.
-
Increased Uptime
By following pre-programmed paths, at an optimized speed, auto-dispatch technology reduces the potential for human error. When combined with anti-sway software or no-fly zone technology, auto-dispatch systems can help minimize downtime for maintenance due to collisions or improper equipment use.
-
Streamlined Operations & Increased Material Flow
Using crane automation technology, rather than manually guiding the load through a work area, helps decrease takt time. Auto-dispatch technology provides automated movement for target positioning from one location to another, while also enabling human assistance for precise end-location positioning. With the push of a button, a load can be automatically sent from one location to another. Then, as the load moves to the programmed destination along a determined route, the operator can work on a different task or start on the next step of the production process for increased efficiency. With the improved speed and accuracy that auto-dispatch technology provides, material can be moved quickly and more efficiently through different stages of the production process to save time and greatly increase productivity.
-
Improved Space Efficiency
Utilizing vertical space to store materials can be necessary when floor space is restricted or at full capacity. An overhead crane with auto-dispatch technology can travel along an aisle between rack structures to a specific location. The automated overhead crane can then manually or automatically lift one object at a time and transport it to the selected storage location. By expanding up, rather than out, a marina bridge crane, for example, can provide significantly more dry dock storage on a smaller footprint to maximize square footage without expensive building additions. Auto-dispatch is a flexible enabler for automated storage and retrieval systems.
Want to learn more about what auto-dispatch technology and crane automation can do for you? Contact us today. We can help you take advantage of this technology in your applications and tell you more about our innovative crane automation solutions, such as our ProPath™ Automated Workstation Crane or Intelli-Guide™ Auto-Dispatch Technology.
AUTO-DISPATCH TECHNOLOGY CASE STUDY
Related Articles
Auto-Dispatch System for Automotive Application
Magnetek Automated Solutions
In automobile manufacturing, time is money. Every minute saved in the process can move another vehicle off the line and into the market. To increase efficiency and reduce process time, a high production automobile manufacturer needed to reduce the takt time for the engine and transmission marriage process. Specifically, the manufacturer was using a manual marriage cell where several processes had to be performed by a single operator. This included picking hardware, selecting traverse time, marrying two heavy components (an engine and a transmission), and installing a wiring harness and attachment hardware.