Industrial Linear Actuators in Automated Manufacturing
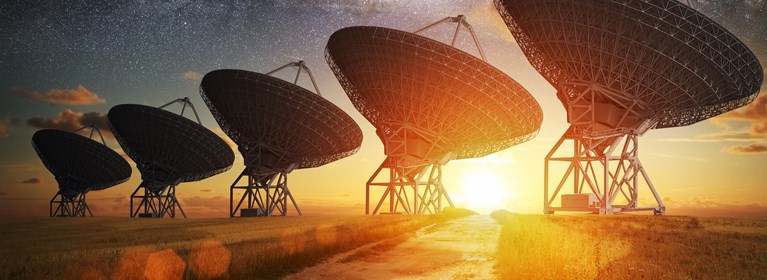
In today's world, motion technology is expected to precisely lift, move, and position heavy loads under extreme or adverse conditions. Industrial actuators are essential if processes call for rotating and pivoting, opening and closing, or keeping a production line moving. The industrial linear actuator is a component in any machine that enables movement by converting rotational motion into push or pull linear motion. These devices are used in automotive manufacturing, process industries, food and beverage processing, material handling, robotics, and other industrial settings where linear motion is required.
When purchasing a linear actuator, it’s essential to choose a product that will fit best with your application and specific demands. Whether you want a high load capacity, a longer duty cycle, or equipment requiring very little maintenance, you’ll need to thoroughly research each type of actuator.
Pneumatic, hydraulic, and electric actuators are the three most frequently used linear actuators. Pneumatic actuators are the most straightforward and affordable option, but they require compressed air, which may not always be available and is very expensive to generate. A hydraulic actuator is generally more reliable than a pneumatic actuator; however, it is significantly more complicated and expensive. Electric actuators are the most flexible option, offering smooth, precise, and maintenance-free motion.
In recent years, electric linear actuators have become increasingly common in various industries to automate their processes due to their precision, safety, small size, and speed. Not only are electric actuators the safer choice, but they also allow manufacturers to build automated process environments. Ultimately, this will help reduce failure rates and improve throughput.
Contact Our Linear Motion Team To Discuss Your Application Needs Today
Challenge: A railroad company used hydraulic-powered moveable bridges to lift rails and move locking pins. However, the hydraulic fluid would leak into the waterway below, and the company received a fine for the spillage every time this happened.
Solution: The company replaced its hydraulics with Duff-Norton’s electric cylinder actuators to solve this issue. Doing so eliminated the risk of spills, environmental contamination, and associated fines.
Challenge: A customer’s plant was out of compressed air capacity but replacing their existing compressor or adding capacity was cost-prohibitive: an estimated $250,000 to $300,000. Furthermore, the pneumatics were inconsistent when they raised eleven fixtures at once, with some raising faster than others and sometimes with a jerky movement.
Solution: The customer replaced pneumatic cylinders in their welding fixtures with reliable and efficient Duff-Norton CMLA-Series actuators. These electric-powered actuators offer far superior performance, providing a movement that is ‘smooth as glass’ and raising/lowering all fixtures simultaneously.
Challenge: A paper company used a hydraulic-powered upender to rotate large, heavy paper rolls. The hydraulics were prone to leakages, which would end up damaging entire rolls of the finished paper. Each leak would cost the company thousands of dollars in scrap material.
Solution: The paper company replaced their hydraulic upenders with Duff-Norton electric cylinder actuators, capable of moving 25-ton loads across a distance of 66 inches. In the four years since making this change, Duff-Norton’s SuperCylinders have delivered a reliable performance with zero scrap, saving the paper company money.